Members Login
Channels
Special Offers & Promotions
Flexicon Technology Optimises Intervet
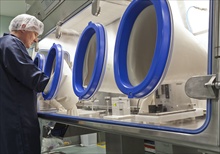
Located in Milton Keynes, MSDAH is a global, research-driven company that develops and manufactures a broad range of veterinary medicines and services. Recently, the company wanted to add additional capacity for processing bacteria/starting materials for the production of animal health vaccines as the 350-employee site was using clean rooms that were causing capacity constraint. As an existing user of Watson-Marlow products, MSDAH saw an opportunity to improve the production methods for these important pharmaceuticals.
"The main issue was to keep the vial filling process sterile and isolated," explains the company's Production Support Manager, Kevin Richardson.
Providing a solution required Watson-Marlow to work in close liaison with Extract Technology, a dedicated manufacturer of isolator units. Focussing on a Flexicon PD12P peristaltic dispensing pump at the centre of the system, a customised flange was engineered to keep the pump drive and control panel outside of the isolator, with only the pumphead sited within the isolator unit.
Both the bacterial seed culture and the excipient (an inactive substance that serves as the vehicle or medium for the drug) are manufactured elsewhere and transferred into the isolator, where they are mixed together and dispensed by the peristaltic pump into small capacity vials held in stainless steel trays. The trays of vials are partially stoppered and placed in the freeze drier. Once this process is complete, the vials are removed and capped before being transferred out of the isolator.
The Flexicon PD12P peristaltic dispensing pump is proving particularly popular for process engineers in the pharmaceutical, diagnostic and biopharm sectors. Its peristaltic filling action means that the product is only in contact with the sterile tubing and the filling nozzle. As a result, there is no possibility for cross-contamination ensuring that no cleaning validation is required. Furthermore, the unit is designed for easy product changeover and offers high suitability for low volume production.
With a filling range from 0.1 to 250ml, the unit provides virtually pulse-free flows with accuracy of ±0.5%. Absolute control is guaranteed to the last drop, where aqueous products can be controlled either by reversing, filling speed or acceleration to offer drip-free operation.
All other system equipment sits beneath the isolator, equating to a significant saving in space, increased efficiency and a more cost effective solution for the customer. The Flexicon filling and capping equipment is built into the isolator in such a way as to be controllable, accessible and easy to maintain.
Watson-Marlow also worked with Extract Technology to engineer the control panel for the pump (based on a Flexicon MC12P master control unit). A foot switch allows the machine operator to stop and start the pump while his or her hands and arms are involved in processes within the isolator. The MC12P controller is connected to a printer for recording production/quality data.
A Flexicon FS10 semi-automatic tabletop cap crimping machine has also been supplied and this is used to seal the vials at rates up to 1000 units per hour if required.
"One of the key things for MSDAH was the integration aspect and the ability of two suppliers to work in close partnership," says Philip King, Sales Manager for Flexicon products. "It was essential that Extract Technology had all the necessary information available to them and were able to work co-operatively from a technical point of view with ourselves, and vice versa. Having worked with Extract Technology previously, we were well placed to meet this need."
Flexicon Liquid Filling offers a range of products from stand-alone units for manual filling, through semi-automatic systems, to fully automatic filling, stoppering and capping machines. The fully automatic systems are customised to fit any glass vial, plastic bottle, test tube, eye-dropper, or non-self standing micro-tube. All machines are designed to operate within sterile environments.
For further information visit www.wmpg.co.uk
Media Partners