Members Login
Channels
Special Offers & Promotions
Affordable LIMS/MRP solution gives small manufacturers quality gains
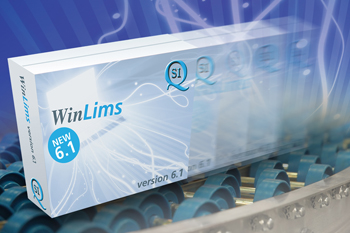
By bundling a Laboratory Information Management System (LIMS) with Materials Requirement Planning (MRP) functionality as part of a single low-cost software solution, the ‘WinLims 6.1 For Manufacturing’ release provides manufacturers fast access to all of the quality data for each material used during a production process. The software also generates the quality data required to release each finished product batch.
“Combining both LIMS and MRP functionality within one application offers manufacturers two quality management solutions for the price of one,” explained Clive Collier, QSI’s managing director. “Our ‘WinLims 6.1 For Manufacturing’ release has been carefully developed to enable medium to smaller manufacturing businesses to close the ‘Quality Circle’ and allow them to track in detail all the materials they use during their production processes.”
“This enables manufacturing companies to quickly prove the quality of their products, increase efficiencies in the manufacturing process, and streamline the commercial aspects of manufacturing. To achieve the ‘Quality Circle’ with a paper based system would be very time- and people intensive which equates to higher costs. The only efficient solution is to use a software application. Traditionally a LIMS and MRP are required and these have to be interfaced to share data to deliver a complete solution.
However, for smaller businesses a key drawback of a combined LIMS/MRP software solution is cost. Both LIMS and MRP are often expensive packages, and most medium to smaller companies find it hard to fund one let alone two of these applications. By launching ‘WinLims 6.1 For Manufacturing’ QSI has solved the cost issue, by providing both LIMS and MRP functionality within one affordable application.”
Having a single data entry point for shared LIMS and MRP data also offers a manufacturer cost saving benefits. Duplication of data is reduced and results in fewer transcription errors.
The MRP functionality offers manufacturers huge benefits of batch traceability and reduced material wastage. There are also major order dispatch, stock control, picking lists and invoice management savings that can be achieved when integrating the MRP and LIMS software.
QSI also provides an innovative no risk rental payment option, WinLims Rental, which enables a company, as long as it is making profits and paying corporation tax, to benefit by reducing their tax burden by the year’s WinLims rental fees. This means that WinLims effectively costs nothing and is essentially ‘free’.
Visit www.qsiuk.com or call +44 1844 208598 for more information.
Media Partners