Members Login
Channels
Special Offers & Promotions
'Ethanol Production by Dry Milling' - New Case Study from Cole Parmer
publication date: Aug 20, 2012
|
author/source: Cole-Parmer
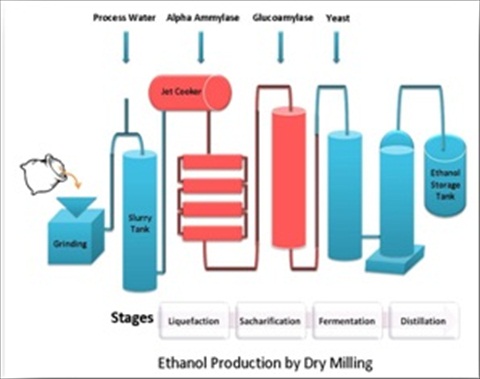
Cole-Parmer's Masterflex® provides accurate and repeatable pumping solution for ethanol production process, enabling precise volume of enzymes to be added continuously.
Ethanol is a versatile alcohol that is used in fuel, beverages and thermometers. Two processes utilized to produce ethanol from grain are dry milling and wet milling. Dry milling plants generate ethanol, carbon dioxide, and distillers' grain, which is used as a high-protein livestock feed supplement. Wet milling plants create these and additional valuable byproducts such as corn syrup, dextrose, and fructose, however they cost substantially more to build and operate than a dry milling plant.
One of the largest sugar manufacturers in India, Saswad Mali Sugar Ltd, use molasses, a by-product generated from their sugar production to produce ethanol. Their dry milling site is capable of generating 846 KLPM of ethanol but they were experiencing process downtime and reduced ethanol concentrations from leakage and blockages in their enzyme dosing pumps. Saswad Mali Sugar needed a solution to reduce their losses. They contacted Cole-Parmer.
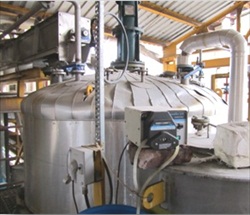
Yeast is added to convert the sugar to ethanol and carbon dioxide. The mash is then allowed to ferment for several days, resulting in a mixture that contains about 15% ethanol as well as the solids from the grain and yeast. The mash is then pumped through a distillation system to separate the ethanol off. Once it leaves the distillation columns, the ethanol is about 95% by volume (190-proof).
Saswad Mali Sugar Factory was initially using diaphragm metering pumps to deliver the glucoamylase enzymes but encountered leakage and blockages in the metering pump system. Mr. Rahul Tilekar, Saswad Mali Sugar, was dissatisfied with their performance. "We started experiencing leakage and blockage in the system within just two months of installation," he said.
Cole-Parmer stepped in and offered fluid handling expertise that proved invaluable. After careful consideration, Cole-Parmer's Application Specialist recommended a Masterflex® peristaltic pump system and pharmed® BPT thermoplastic elastomer tubing
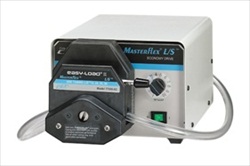
About Saswad Mali Sugar Ltd
Down in the depths of the peak district resides a reputed sugar manufacturing company, Saswad Mali Sugar Factory Ltd. The company has set up a 30 klpd molasses based distillery at Malinagar. The unit manufactures 900 KLPM of rectified spirit, 846 KLPM of ethanol, 90 KLPM of impure spirit and 15 KLPM of fusel oil.
Further details available at http://saswadmalisugar.com/
About Cole-Parmer
Cole-Parmer has been a leading global source of laboratory and industrial fluid handling products, instrumentation, equipment, and supplies since 1955. Our product lines, including popular brand names such as Masterflex®, Oakton®, and more, are sold through company-owned customer channel outlets and a strong network of international dealers. Cole-Parmer responds with excellence to customer needs, and offers application expertise and technical support. For more information, contact Cole-Parmer, Unit 3 River Brent Business Park, Trumpers Way, Hanwell, London W7 2QA. Call +44-(0)20-8574-7556.
For further information visit www.coleparmer.co.uk
Media Partners