Members Login
Channels
Special Offers & Promotions
Bristol Composites Institute detail their studies of Advanced Composite Materials using the Deben 200N tensile stage.
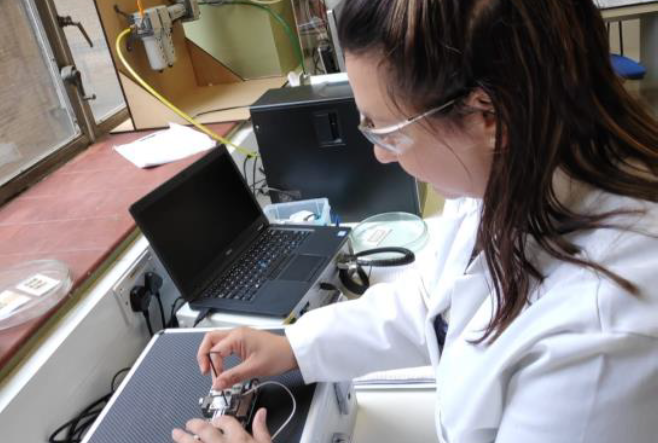
Deben, a leading provider of in-situ testing stages together with innovative accessories and components for microscopy, reports on how Bristol Composites Institute of University of Bristol use the Deben 200N in-situ tensile stage to study Advanced Composite Materials for Aerospace applications.
The Bristol Composites Institute (ACCIS) is a department of the University of Bristol looking at materials, structures and manufacturing and design. ACCIS hopes that their work will assist in meeting the demand for high performance, multifunctional materials in a sustainable way. The department focuses on the study of Advanced Composite Materials and the related applications for Aerospace Engineering. To quote Professor Michael Wisnom (the Director of ACCIS) the goals of the institute are to ‘bring together composites activities across the University of Bristol; based in the Faculty of Engineering and linking to the Faculties of Science and Health Sciences. Our vision is to be a world-leading institute for composites research and education, combining cutting-edge fundamental science with strong industrial links for exploitation and technology transfer. ACCIS is a focus for collaboration internally, nationally and internationally.’
We had the pleasure of speaking to Konstantina Kanari who is working on toughening composite laminates using hierarchical electrospun and electrosprayed nanofibre/particle interleaves at ACCIS. We asked Konstantina to describe her work and its applications: ‘Sectors like the aerospace and automotive industry use laminated composite materials to achieve lighter and, at the same time, toughened structures. This approach will result in reduced fuel consumption and therefore fewer emissions, hence it is more environmentally friendly. However, one of the biggest issues with the use of composites in load-bearing applications is that laminated composites suffer from delamination and low fracture toughness. Various approaches are currently pursued on the improvement of these properties, with one approach being the use of micro- and nanofibrous interleaves as plies. The interleaves have been shown to improve the toughness of laminated composites, mostly due to their bridging of crack zones. Furthermore, nanoparticles have been added in laminated composites to enhance the stiffness of the material and increase its fracture toughness. The incorporation of nanoparticles leads to the enhancement of local strain to failure within fracture zones due to a toughening mechanism called crazing.’
Further describing the end goal of her work ‘This project aims to improve laminated composites’ toughness by combining all the above mechanisms. Therefore, in this research electrospun/electrosprayed nanofibrous interleaves are to be used, nanoparticles are to be included in the composite material and different sizes of fibres and particles are to be tested. This research project is inspired by what is seen in nature, and aims to use different nanomaterials in a hierarchical way to form improved materials. Nevertheless, the improved toughness of the composites should be achieved without adding excessive weight to the final product.
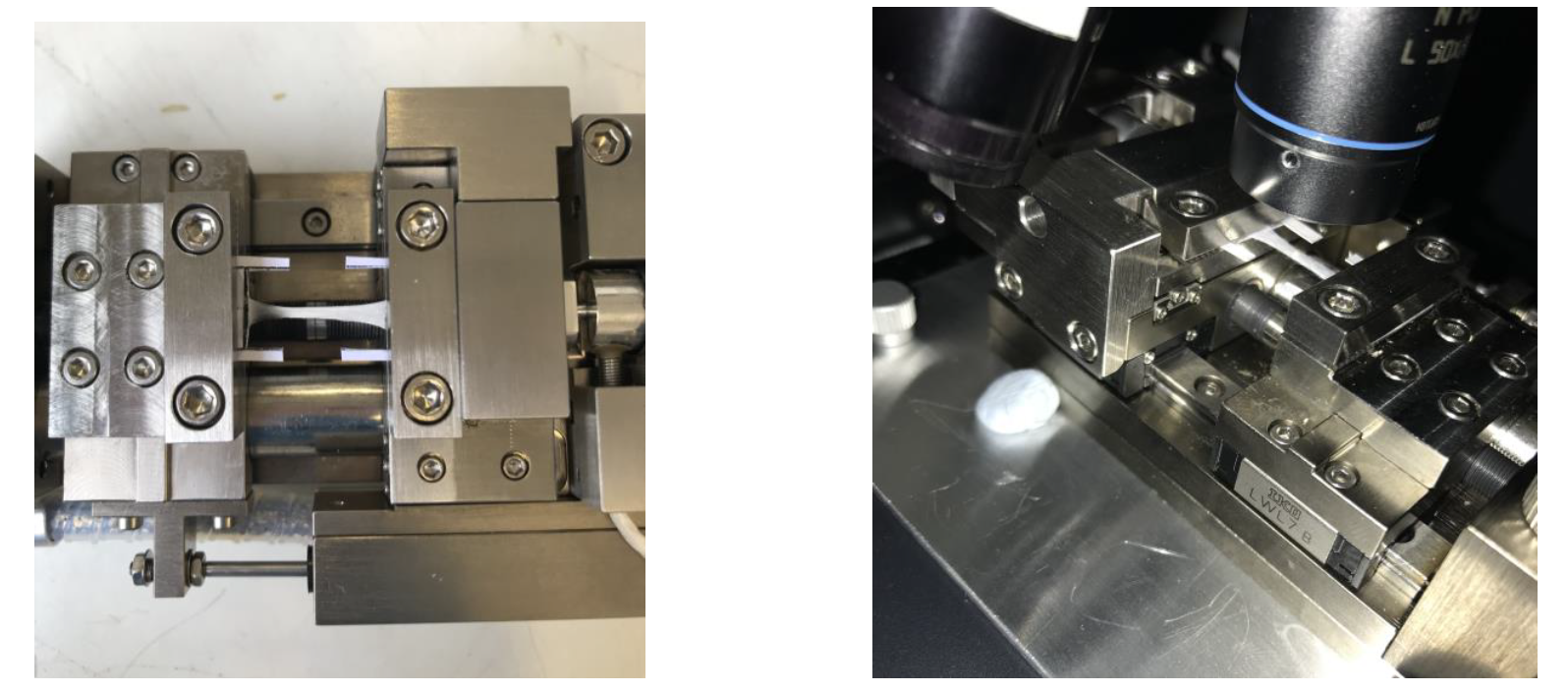
Konstantina describes her experience using the Deben 200N tensile stage: ‘I use the Deben stage to test the tensile properties of electrospun nanofibrous networks that will be used as interleaves in laminated composites. The networks cover a range of properties, e.g. aligned or random orientation, with or without the addition of nanoparticles etc. Furthermore, the Deben stage is to be used during testing with Raman spectroscopy to try and identify if the nanoparticles are embedded in the nanofibres.’ We asked her to identify the positives of using the Deben stage: ‘The load cell’s high sensitivity means that small force changes can be detected and measured, which other stages have failed to do.’
References
http://www.bristol.ac.uk/composites/
more on the Deben 200N tensile stage
Deben are a precision engineering company, established in 1986. They specialise in the field of in-situ tensile testing, motion control and specimen cooling for microscopy applications. The main product groups include: motor control systems, in-situ micro-tensile stages, Peltier heating & cooling stages, detectors for SEMs and electro-static beam blankers.
Deben provide consultancy, design and prototype manufacturing services. In house facilities include SolidWorks and SolidEdge 3D CAD and COSMOS finite element analysis software, CNC machining, electronics design and manufacture and software design using Visual C++, Microsoft.net and DirectX.
Deben UK Ltd. is a subsidiary company of UK based Judges Scientific plc.
View Company Profile and Recent News
Media Partners