Members Login
Channels
Special Offers & Promotions
Georgia Tech Chooses TAP
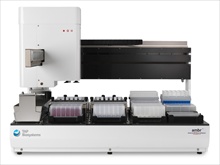
The ambr system, which closely replicates the characteristics of bioreactors at micro scale, will be used by scientists in Georgia Tech's new Stem Cell Engineering Center to determine optimal conditions for culturing mouse and human pluripotent stem cell lines, which could be used in drug discovery and cell therapy applications.
Additionally, the ambr system will be used over a five year programme to help train at least 30 NSF (National Science Foundation) funded IGERT (Integrated Graduate Education Research Training) trainees in stem cell production. This will allow these researchers to understand how to scale and control stem cells into clinically relevant numbers and will develop the next generation of experts in stem cell biomanufacturing.
Dr Todd McDevitt, Director of the Stem Cell Engineering Center at The Georgia Institute of Technology said: "Manufacturing stem cells in bioreactors is a goal for cost-effective production and to date we have studied stem cell differentiation using rotary orbital suspension culture. This type of culture method is not as practical for bioprocess modelling as it is more time consuming and almost impossible to evaluate a wide range of media and culture conditions in parallel."
Dr McDevitt added: "Our research requires automation which offers a rigorous approach and we initially considered developing our own equipment until we heard about the ambr system. The ambr system is ideal for studying a large number of parameters that could affect stem cell growth and differentiation and we will use the ambr technology to predict stem cell performance in large scale bioreactors."
Dr Barney Zoro, ambr Product Manager at TAP Biosystems stated: "The cost of generating many types of stem cell at clinically relevant scale is currently prohibitive. Development of suspension culture processes will allow production of larger quantities of more affordable stem cells and we're pleased that this leading institute has chosen the ambr system to optimise these important stem cell bioreactor cultures. Through their research, the ambr system could be instrumental in helping to deliver cell lines for drug discovery assays, as well as enabling allogeneic cell therapies to become more readily available."
For more info visit www.tapbiosystems.com
Media Partners